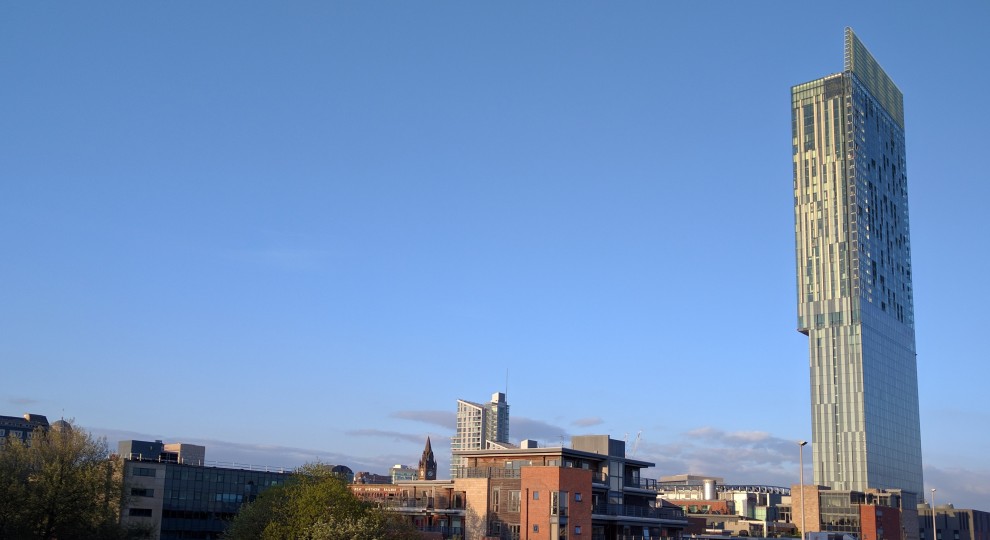
Wind Induced Noise on Building Facades
A 47 story, mixed use skyscraper in Manchester attracts the attention of anyone within a 3 mile radius. It towers above the City skyline but that’s not the reason people are drawn to it. Neither is the award-winning architecture.
Beetham Tower isn’t getting the attention of Mancunians because of what people can see. It’s what they can hear that turns heads. And what they can hear is a high-pitched humming sound. The culprit is a 9m high feature perched at the very top. Consisting of a number of glass louvers, it causes a resonance that’s audible from 3 miles away. Given Manchester’s population density, over 100,000 people are affected every time it whistles.
We can only imagine the headaches and liability issues it has caused for everyone involved. So what do you do? We take a closer look at why some facades stay silent, some like to make their presence heard, and what can be done to silence them if they do.
What Causes Wind Induced Noise?
Wind noise itself is hard to isolate. There are a number of factors that come into play and how they line-up is a bit of a mystery which needs unraveling. The exact same design in one location might be excruciatingly noisy yet silent when sheltered by a neighboring building in a different location. The prevailing winds in Christchurch are east-north easterly. In Auckland, they come mainly from the southwest.
The best way to understand the risk of wind noise for a design is to understand the mechanisms behind it. Then design considerations can be selected to best mitigate the risk. These key mechanisms are:
-
Vortex Shedding
-
Helmholtz Resonance
-
Structural Vibration
Vortex Shedding. When wind hits a structure alternating vortices are formed at a specific frequency, often leading to a vibrational load. The result is an aeolian tone or whistle, measured in hertz. Large resonances can occur in situations where the vibration frequency is the same as the natural resonant frequency of the facade element. In other words, the disturbed airflow that is forced around (or through) the facade generates the same frequency as the facade itself.
For example, if you were to take a tuning fork that vibrates at a particular frequency and blew air over it in a way that leads to vortex shedding off the end, when that distorted wave matches the frequency of the tuning fork, it would hum the same as if you were to tap it.
Helmholtz Resonance. This is essentially air increasing and decreasing in pressure rapidly within a fixed volume, often referred to as wind throb. So it’s the result of air passing over a single opening (both entry and exit) causing the air in and around the opening to vibrate as the air inside compresses and decompresses. You can recreate the effect by blowing across the top of a bottle neck or opening just one window in a moving car.
Structural Vibration. Sound is an energy made by vibrations. Not that all structural vibrations make a sound though. In some cases it can be worse (see Tacoma Bridge). This might be of a lesser concern for the most part but as it can’t be ignored, as a later balustrade example will highlight.
Whilst we can’t pinpoint exactly when and why any of the 3 above will cause a particular noise, we do know from experience that the likelihood will change depending on the design and products used. Interestingly, we can even quantify the risk for particular products and materials when certain environmental factors are present.
Wind Induced Noise in Common Products & Materials
Experience teaches us which frequently used products and materials are more or less likely to make a noise:
Extruded Aluminum Sunshades (i.e. louvers). Low potential for wind noise. These are generally issue free due to their distance from the building, level of thickness and the spacing between the louvers.
Perforated Sheet Metal. High potential for wind noise. Perforated sheets are known to cause wind noise, the extent of which is dependent upon several factors, such as the size of the perforation.
Balustrades. Medium potential for wind noise. There has to be multiple contributing factors for balustrades to make a noise. That can happen though, as we’ll detail shortly.
Bespoke facades are a different matter. The potential for wind noise varies greatly but is, in part, influenced by the choice of material. We know timber to be of a very low risk for noise. The same goes for mesh. We’ve never had any issue with plastics to date but believe there could be issues given the right (or wrong) set of circumstances, so it needs considering from first principles, as do custom metal facades.
There is an elevated risk of noise when using either glass or mesh, and caution is advised. This is particularly true where wire growing frames are used for living walls, as the initial non plant-covered wire can act like a guitar string.
The Problem with Perforated Screens and Wind Noise
It makes sense that a perforated screen can make a noise. After all, there’s a whole section of an orchestra for instruments relying on wind and holes to make a tune. The problem with noise from perforated screens is it’s less orchestral and more like a 5 year old attempting to play the recorder for the first time. So what to do?
Perforations sizes less than 10mm should be avoided. Broadly speaking, the smaller the perforation size then the greater the potential for noise. Larger holes have a lower frequency and need more air to make them scream.
The shape of the perforation is equally important. A perfect circle is far more likely to whistle than a hexagonal shape.
Then there’s uniformity. Where multiple perforations are of the same shape and size, uniformly distributed over the facade, there is a high potential for noise. The introduction of randomness or variation in the design decreases risk as you might get only a % of the sheet causing problems, which is less than a 100% (obviously).
Finally, any gaps between the screen and the mounting frame should be at least 10 mm wide.
The Problem with Balustrades and Wind Noise
Balustrades are often found in areas of windflow where there is a higher risk of wind induced noise, such as a corner balcony on a high level apartment block, where they project outside the turbulent wash zone found closer to the building skin, in an area of increased airflow speed.
If the vertical balustrades are slender, round or near round, or even flat, they’re considered highly likely to produce vortex shedding. This was the case for an apartment block in Auckland, where the flat fins of the balustrade produced an unpleasant tone that varied as the wind changed speed and angles. All tones were equally unpleasant and annoying for the occupants whose bedrooms were closest to the balustrades.
In another Auckland example, an architectural metalworker was left scratching his head as to what could cause balustrades in a multi-level apartment block to break. They had broken clean through in the middle yet had no sign of impact. The culprit was vortex shedding at a very high frequency, leading to the balustrades becoming fatigued due to structural vibration. It’s a bit like bending a paperclip back and forth. Pretty soon it will snap.
That’s what wind can do. The potential for unseen structural degradation of a critical building safety element needs to be considered.
The Facade Wind Noise Risk Matrix
When we provide design assistance, we need to know the design won’t make a noise. To put it bluntly, we don’t want to be liable. If we install balustrades on a hotel that makes a nose, guests will complain. Then the hotel will complain to the architect. Who will complain to us. Followed by us complaining to our accountants. And we definitely don’t want to speak to them.
To mitigate against this, we’ve developed the facade wind noise risk matrix. It quantifies the risk of noise based on the probability of annoyance levels and wind gusts. For example, if a hotel has a balustrade next to the bedroom and is in a location likely to receive gusts over 100km/h - we know there’s a need for some testing. Conversely, a ground floor perforated screen with perforated circles of 15mm won’t require any testing.
If the risk is classified as extreme and no changes can be made to the design to change that, the matrix will recommend testing. It’s the prudent thing to do and also the most cost effective. Which is exactly why wind testing was conducted before we installed a facade in a high end apartment building on Kepa Road, Auckland.
Outlook Apartments features a veil of 38mm anodized tubes at regular centers, spanning between the floor levels. With the tubing going around the corners and positioned close to the building, it jumped out as a likely candidate for significant vortex shedding.
This was confirmed when we ran a CFD analysis. What the analysis couldn’t tell us was whether the vortex shedding would generate wind noise or not. That required a 1:1 scale wind tunnel test.
It had to be a 1:1 scale test too, as it's impossible to get the frequencies right when scaling down. With no facilities in New Zealand capable of doing this, we went to Australia and found a wind tunnel we could make work. It still needed the nozzles adapting and wasn’t perfect as we required it to do something it wasn’t designed for.
The results led us to two conclusions. Firstly, the anodized tubes would not make a noise, which was a huge relief.
Secondly, we would need our own wind tunnel, designed to our specifications and able to fully test 1:1 scale models. As more and more medium and high density housing, multi-level commercial complexes and high rise buildings are constructed, the need for testing would only grow. To mitigate the risk of designs making a nose would require an imperfect testing regime overseas unless we built our own wind tunnel, here in Invercargill. So we did. You can take a closer look at the Southern Hemisphere’s only specialist wind testing facility for facades here.
We now routinely test new products and designs for wind noise. Where we’ve developed a standardized range of patterns we know might be at high risk, such as the dapple range of perforated screens, we assign them a rating so they can be specified with confidence, or serve to alert the architect that depending on where the product is used, further testing is advisable.
Taking this approach will ensure no-one has a Beetham Tower on their hands. Because we don’t want that and we doubt anyone else does either.